Les produits et services débit, usinage…
Aluminium
PVC
Bois
Services
Le groupe BDM en quelque mots
Bjm Dubus Machines est la holding réunissant le fabricant allemand BJM et la société DUBUS basée en France.
Ensemble, nous sommes leader industriel et fabricant Numéro 1 mondial de centres de débit & usinage automatisés pour le travail des profilés
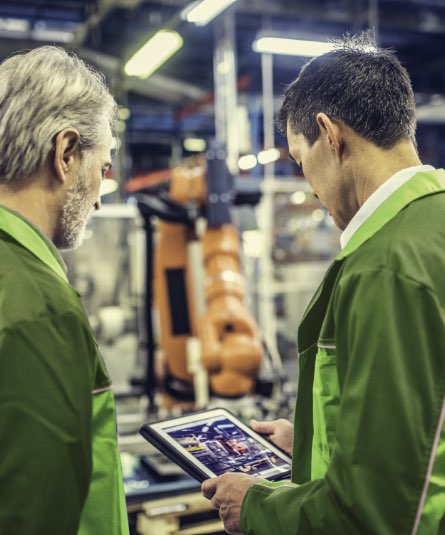
Les Services aux Clients proposés par BDM
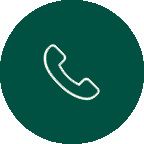
Hotline assistance technique
& maintenance
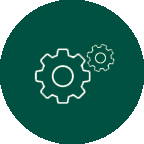
Pièces détachées
& outillage
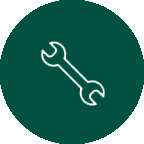
Rétrofit, modernisation,
transfert machine
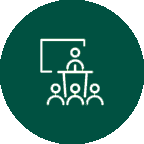
Formation & support